Perlite is one of the most overlooked insulating materials, especially as it offers numerous advantages over other organic and inorganic insulation materials.
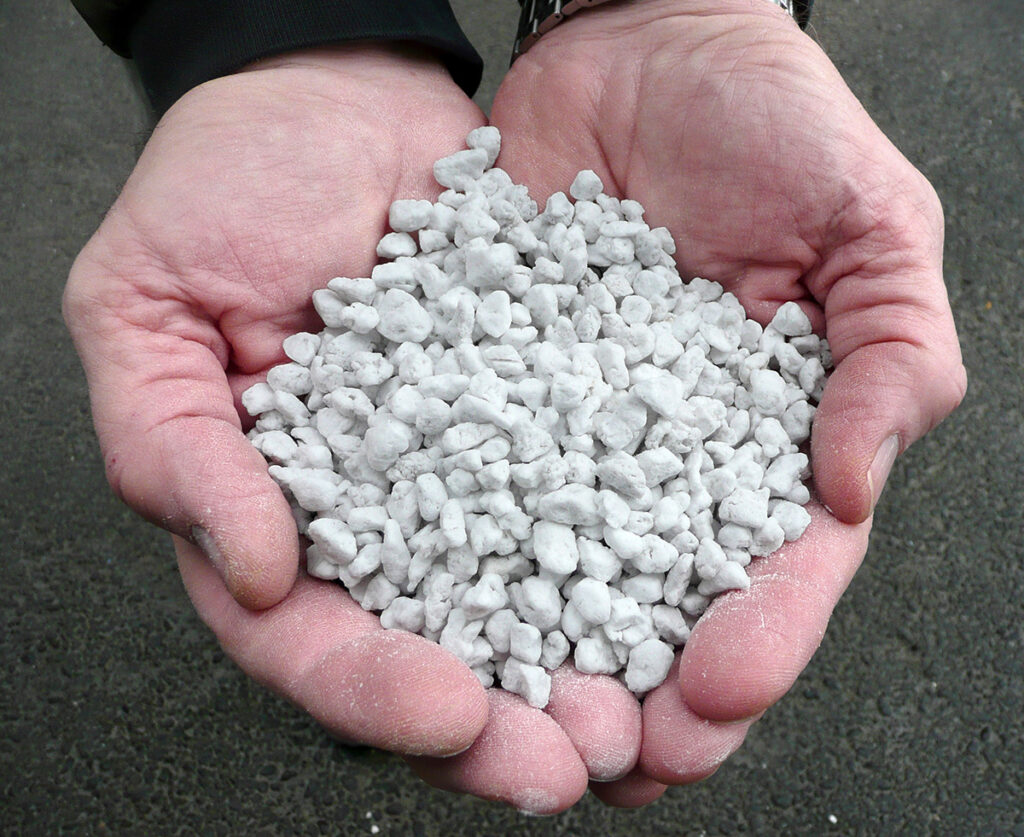
In an era of growing concern for the impact that building materials and products have on the environment, the choice of which materials to use is increasingly informed by relative performance and sustainability metrics. An extensive review of international literature and comparative technical studies finds that perlite is very much seen as a sustainable, natural and user-friendly alternative to competing organic and inorganic insulating materials, like PUR-foam and EPS coming from non-replenishable sources and mineral wools. Global academic research and official technical reviews from certified national bodies argue decisively in favor of perlite as having a minimal Global Warming Potential (GWP) and that perlite-based insulation offers consistent thermal performance over the application lifecycle while at the same time protecting structures from fire. The information presented here relies on data compiled from a range of independent international bibliographies focusing on the performance of various insulation materials over time, the efficient use of raw materials and waste generated, and their relative fire-resistant qualities.
Introduction
Perlite is a naturally occurring, siliceous volcanic mineral that expands when heated to form a froth of tiny glass bubbles of entrapped air. The resultant ultra-lightweight material, referred to simply as expanded perlite, is durable, non-combustible (Class A1/DIN 4102), inorganic, and ultra-lightweight with a bulk density range of between 40 Kg/m³ and 140 Kg/m³ (2.5–9.0 lb./ft³). Expanded perlite has low thermal conductivity at 0.044 W/mK (0.023 BTU/hr·ft·°F) at ambient conditions, with an R-value of approximately 3.0–3.5 per inch at a mean temperature of 40 deg F (4 deg C) for product 4.1– 7.4 lb/ft³ (66 –118 kg/m³). It is resistant to chemical attack, odorless, pH neutral and can be produced to comply with ASTM C332i and ASTM C549. Construction grade expanded perlite replaces chemical insulators and products such as expanded polystyrene (EPS), extruded polystyrene (XPS), and polyurethane foam. Such chemical products are highly combustible, contain Volatile Organic Compounds (VOCs), are organic and deteriorate with time.
For example, the performance of cellular plastic foams as insulating materials is not stable over the long-term (see Figure 1). Both EPS and XPS deteriorate with time in two main stages.1 In the primary stage (under 5 years), air from the outside penetrates the insulating material and replaces the insulating gas inside each enclosed cell. In the secondary stage (5 years and up), the gases that penetrated the internal air bubbles are slowly lost to the outside without being replaced, resulting in gradual shrinking of volume. The morphological change and the replacement of low conductivity gas with air causes an overall decrease in thermal resistance of the foam-based insulation.
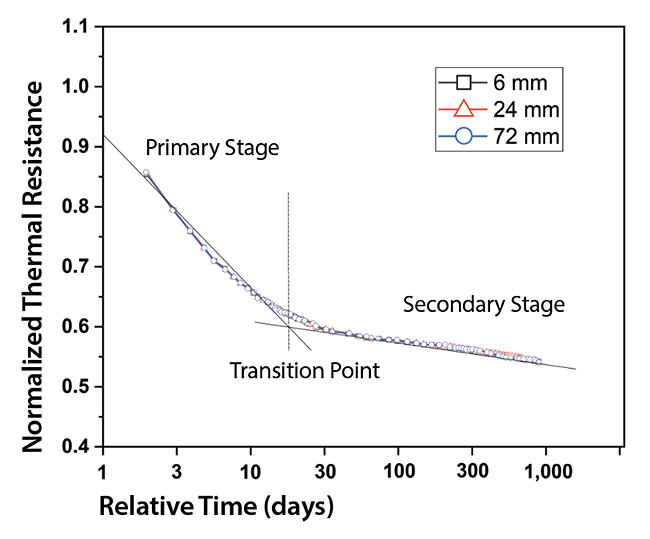
Aging/Drop of Thermal Insulation Performance of Expanded Polystyrene/Polyurethane
- Thermal resistance of expanded polystyrene decreases by up to 43% (from 2.485 m2∙K∙W-1 to 1.424 m2∙K∙W-1) after roughly 5,000 days from production.[2]
- Thermal resistance of rigid polyurethane falls by up to 27.5% (from 2.579 m2∙K∙W-1 to 1.897 m2∙K∙W-1) after 5,000 days.[2] The same trend has been identified for polyurethane (PU) foam insulation in refrigerator panels.[3]
By contrast, perlite is dimensional, stable and keeps its insulating performance 100%. It maintains its structural integrity and retains stable thermal conductivity for the entire lifetime of the building.
Perlite: The Safe and Fully Natural Material
Both unexpanded and expanded forms of perlite are fully natural, inert, mineral-based materials. No long-term health effects have been linked to perlite mining, processing, or application and installation activities, provided that the prescribed occupational exposure limits (OEL) and means of using Personal Protective Equipment are observed. For more information, see the relevant information published by the Perlite Institute. iii
i • ASTM Standard C332-99, 2017, “Standard Specification for Lightweight Aggregates for Insulating Concrete,” ASTM International, West Conshohocken, PA, 2017, DOI: 10.1520/C0332-99 and ASTM Standard C549-18, 2018, “Standard Specification for Perlite Loose Fill Insulation,” ASTM International, West Conshohocken, PA, 2017, DOI: 10.1520/C0549-18
ii • ISO 11561:1999, “Aging of thermal insulation materials: determination of the long-term change in thermal resistance of closed-cell plastics (accelerated laboratory test methods)”, International Organization for Standardization, Genova, CH, 1999
iii • “Perlite, the Safe and Fully Natural Material.” See Perlite Institute webpage, https://www.perlite.org/perlite-the-safe-and-fully-natural-material
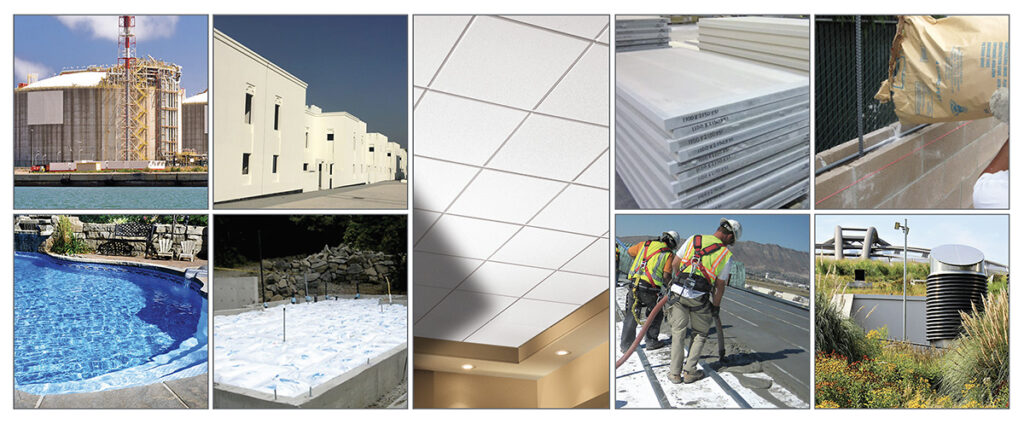
Embodied Energy and Embodied Carbon
Embodied energy (EE) and embodied carbon (EC) constitute two important metrics for examining the relative amount of energy involved in manufacturing a product. Embodied energy accounts for the energy used for extracting and processing of raw materials, manufacturing, transportation and distribution, and final construction or assembly. Embodied carbon is the sum of fuel-related carbon emissions (i.e. embodied energy that is combusted, but not feedstock energy retained within the material) and process-related carbon emissions (i.e. non-fuel related emissions that may arise, for example, from chemical reactions). This document follows a cradle-to-gate approach, in which the impact of the product is considered from the point of extraction of the raw materials up to distribution of the finished goods.
Figure 2 and Figure 3 present embodied energy and embodied carbon, respectively, under the cradle-to-gate boundaries, for perlite and other insulating materials.
Expanded Perlite has minimal embodied energy and embodied carbon compared to all other organic and inorganic alternatives. The values for raw perlite ore are 0.66 MJ/kg and 0.03 kg CO2 eq/kg, respectively.
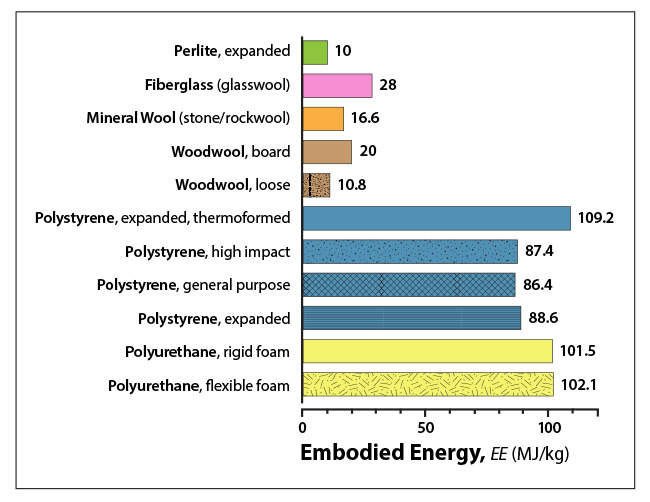
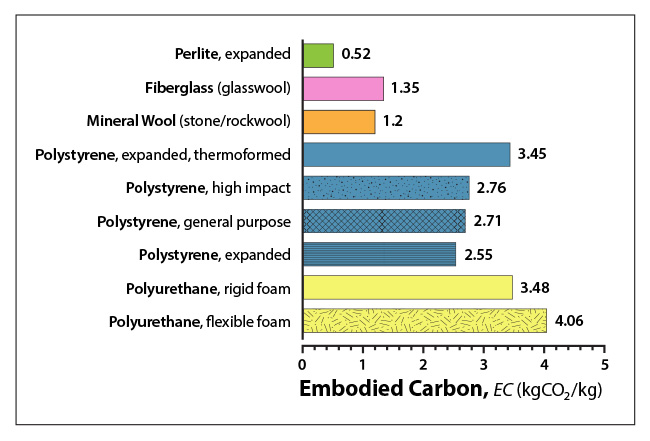
Embodied Energy (Fig 2) and Embodied Carbon (Fig 3) of raw and expanded perlite and other insulating building materials [4], [5]
Global Warming Potential and Applications
Global Warming Potential (GWP) is the appraisal of a material’s relative contribution to greenhouse gas emissions, such as carbon dioxide (CO2), methane (CH4), and ozone (O3). GWP is calculated at the manufacture (Stage A), use (Stage B), and end-of-life stages (Stage C), and it is calculated as the sum of emissions of the greenhouse gases (CO2, N2O, CH4 and VOCs) multiplied by their respective GWP impact factors.
GWP of expanded perlite and other insulating materials calculated on mass and volume basis is presented in figure 4 and Figure 5, respectively. As shown in Figure 4, expanded perlite offers an extremely favorable GWP when compared on a mass-to-mass basis to similar alternatives such as mineral wool, EPS, fiberglass, extruded polystyrene and polyurethane foam. It accounts for only 0.52 kg CO2 equivalent, which is five times lower compared to polystyrene at 2.70 kg CO2 equivalent.
A similar observation (Figure 5) can be made when GWP values are compared on a volume basis per m³ of material. In that case, fiberglass presents the least impact with 12.8 kg CO2 equivalent per m³ of material, while perlite comes in third at 60.1 kg CO2 equivalent. This is explained by the extremely low densities of both EPS and fiberglass in comparison to that of expanded perlite considered.
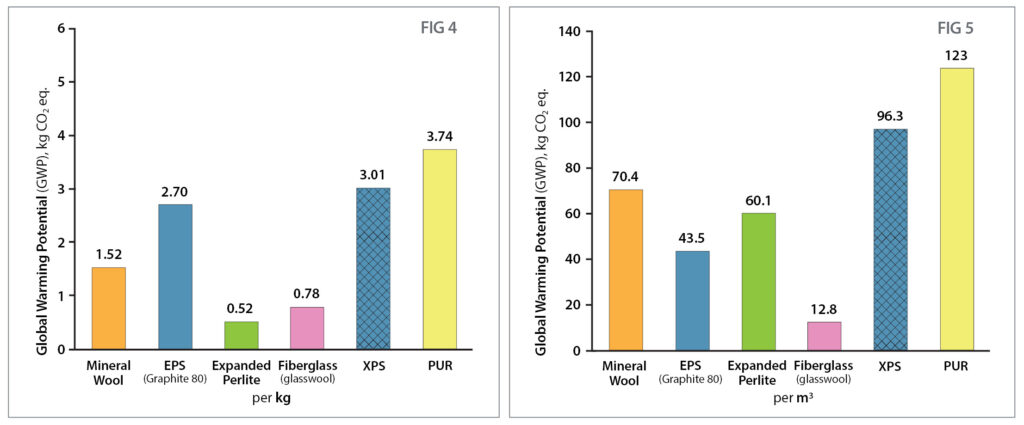
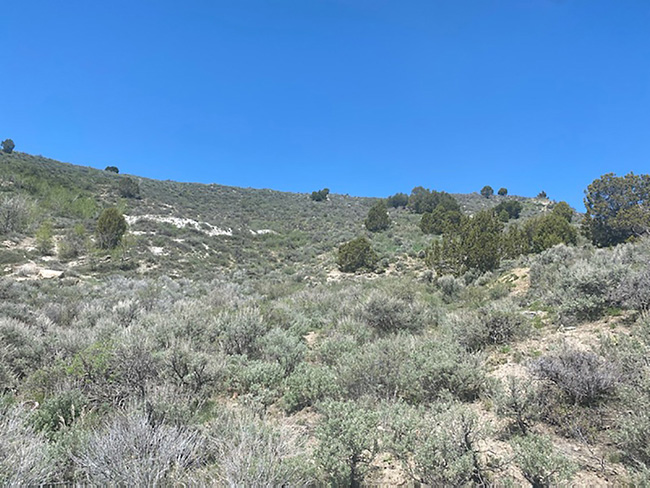
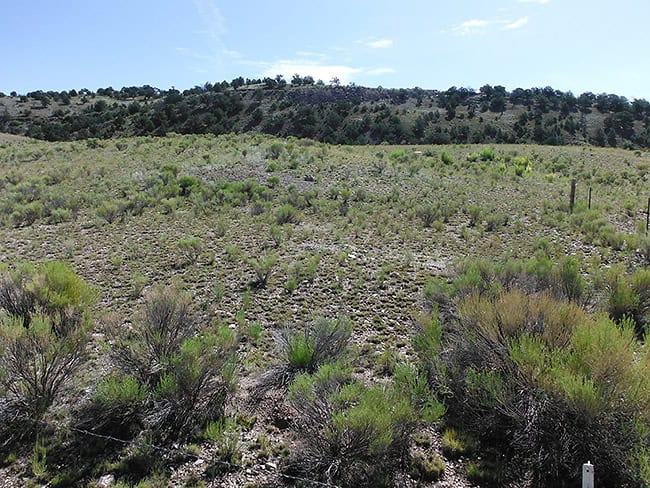
Reclaimed perlite mining operations. After ore extraction, stockpiled topsoil is replaced and the landscape is replanted with native plants and grasses. Pictured Above: Reclaimed sections of the Hess Perlite Mine in southeast Idaho, USA and the Dicalite Perlite Mine in central New Mexico, USA.
Table 1 presents key environmental metrics associated with ‘cradle-to-gate’ manufacturing processes for common insulating products including raw material extraction, transportation to the processing facility, and final manufacturing (EN 15804iv). Ozone Depletion Potential (ODP), Photochemical Ozone Depletion Potential (PODP), Eutrophication Potential (EP), and Acidification Potential (AP) are important metrics reflecting the relative environmental impact of construction products. Among all the commonly used building insulation materials compared, expanded perlite has the least ODP, PODP, EP and AP values calculated on either a mass or volume basis, and the least environmental impact overall. (Marginally lower values for PODP of fiberglass and EP of EPS are only evident when calculated on a volume basis as a result of their extremely low densities.)
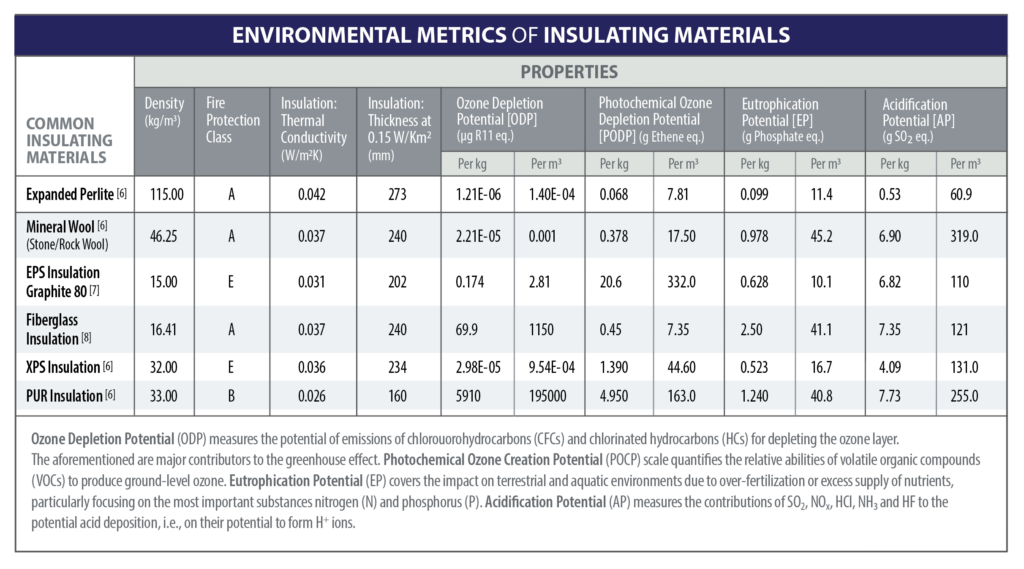
Efficient Mining, Expansion & Transport
The global perlite industry actively mines a total of less than 8 square km (3 sq miles) annually, as noted in a relevant Perlite Institute brochure.v Perlite mining and processing takes place close to the surface with minor quantities of overburden and waste produced. According to the 2021 USGS report, annual worldwide perlite extraction is approximately 3.1 mil. metric tons and known reserves are estimated to be in excess of 350 mil. metric tons; annual production represents less than 1% of the known world reserves.1 The list of reserves continuously expands with new deposits discovered.
Lightweight perlite construction grade aggregate is expanded at perlite factories to an average 12 times its original volume. Thus, mining volume, energy and environmental impacts are 12 times less compared to ordinary unexpanded aggregates, like sand and gravel, on a volume-to-volume basis. Expansion occurs as a single-step thermal process and the energy involved is often as low as 1.5–2.0 MBTU per ton.
Perlite manufacturers are located around the world. It is a locally available building material in almost every country worldwide. Local distribution of expanded perlite is viable and LEED compliant when the distance from the manufacturing plant is less than 500 Km (310 miles). Transportation is carried out via road, rail, and ocean-going vessels.
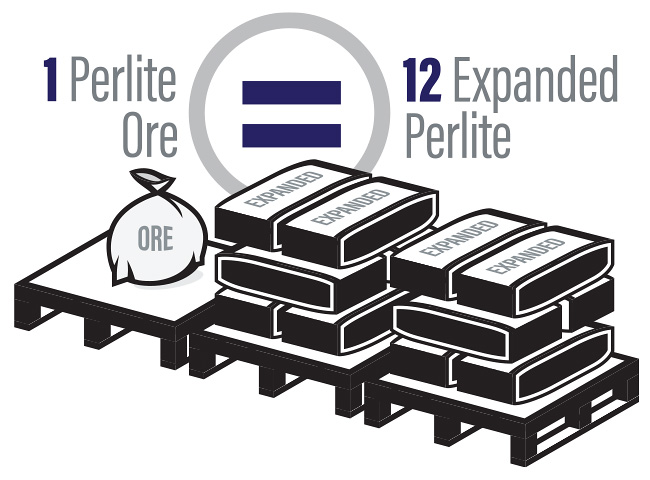
Selected Applications
PERLITE LOOSE-FILL WALL INSULATION
Expanded perlite offers very favorable environmental attributes combined with optimum thermal performance. Low U-values (thermal transmittance values), offer easy pathways to compliance with increasingly stringent building performance requirements. The U-values achieved are maintained over the lifecycle of the building. Construction grade perlite easily lasts for the typical lifetime of a building (usually 50 years) and will continue to offer the same U-value for many years beyond, which is not the case for petroleum-based insulators which experience degradation over time and a decrease of their U-value. Additionally, and in contrast to perlite which is non-combustible, they are a high fire hazard threat. Optionally, expanded perlite may be coated to render it hydrophobic and reduce the moisture absorption.
PERLITE LIGHTWEIGHT INSULATING CONCRETE
Perlite lightweight insulating concrete consists of a mix of construction grade expanded perlite aggregate, cement and optionally sand. Perlite lightweight insulating concrete reduces building dead loads; hence structural requirements (beams, columns). It further displaces the total volume of concrete (a known contributor to greenhouse gas emissions), as well as reinforcement, which further saves on natural resources. Perlite lightweight insulating concrete is the most widely available thermal insulating concrete with a very low thermal conductivity value of k = 0.07 – 0.08 W/mK (0.04 – 0.046 BTU/hr·ft·°F). Perlite lightweight insulating concrete roofing offers higher thermal insulation performance coupled with the durability and strength of concrete.
OTHER BUILDING PRODUCTS
Construction perlite is used by numerous building material manufacturers to produce sustainable products, such as thermal insulating and fire-resistant plasters, acoustic products, and lightweight construction products (mortar, glue, paint, adhesive, etc.).
PERLITE FOR BUILDING LANDSCAPE APPLICATIONS
Fine grade perlite is used for landscape applications as an inorganic, pH neutral, fully natural water-retaining soil additive to reduce overall irrigation demand by 50% in sandy soils, as proven in a recent Perlite Institute study. This reduces the demand for irrigation water and encourages larger beautification areas.
Coarse grade perlite is used as a lightweight soil conditioner to reduce dead load on building planters or roof gardens. This allows for bigger, deeper and greener podiums and raised bed landscaping. Due to its grain size coarse perlite improves the soil structure, adding more “loft” and “texture” to keep the soil well aerated and loose.
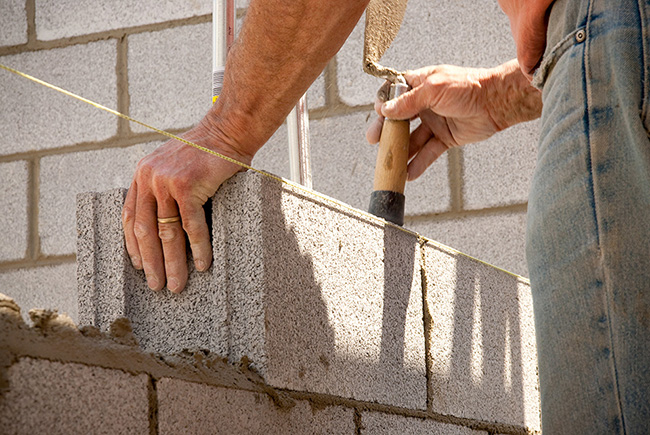
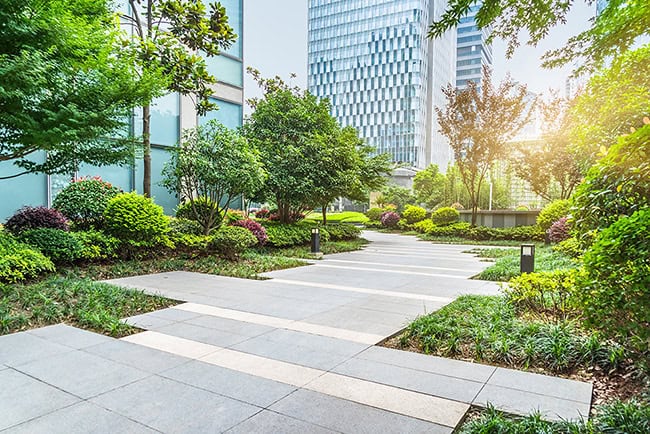
Not only is expanded perlite sustainable, it’s enduring. Photo 1: Perlite loose fill block insulation is easy to place and easily performs for the life of the building. Photo 2: Urban landscapes need to be viable for the long term—unlike short-lived compost, native soils amended with perlite provide structural and water-retentive improvement indefinitely.
Summary
- The environmental aspects of construction grade expanded perlite insulation improves the overall sustainability of modern building construction. Perlite offers a minimal Global Warming Potential (GWP) and favorable Embodied Energy (EE) and Embodied Carbon (EC) factors in comparison with other common insulating materials when calculated on a mass basis.
- Perlite presents a considerably lower environmental footprint and minimum Ozone Depletion, Photochemical Ozone Depletion, Eutrophication Potential, and Acidification Potential in comparison to other competing organic and inorganic building insulation materials.
- Perlite offers thermal insulation and stable U-value performance that lasts for the entire design life of the building.
- Perlite lightweight concrete is ultra-lightweight, which allows for the reduction of structural building elements during the design/construction phase.
- Perlite is non-combustible and fire-resistant.
- Perlite products do not pose health risks commonly associated with other construction products (i.e. silicosis and VOCs).
- Emissions associated with transport are reduced because perlite is lightweight and is either locally or regionally available.
- There are significantly fewer natural resources consumed per volume of finished product.
BIBLIOGRAPHY
[1] H. Choi, H. Ahn, G. Choi, J. Kang, and J. Huh, “Analysis of Long-Term Change in the Thermal Resistance of Extruded Insulation Materials through Accelerated Tests,” Appl. Sci., vol. 11, 2021.[2] H. J. Choi, J. S. Kang, and J. H. Huh, “A Study on Variation of Thermal Characteristics of Insulation Materials for Buildings According to Actual Long-Term Annual Aging Variation,” Int. J. Thermophys., vol. 39, no. 1, pp. 1–11, 2018.
[3] K. E. Wilkes, D. W. Yarbrough, W. A. Gabbard, G. E. Nelson, and J. R. Booth, “Aging of polyurethane foam insulation in simulated refrigerator panels – Three-year results with third-generation blowing agents,” J. Cell. Plast., vol. 38, no. 4, pp. 317–339, 2002.
[4] G. Grazieschi, F. Asdrubali, and G. Thomas, “Embodied energy and carbon of building insulating materials: A critical review,” Clean. Environ. Syst., vol. 2, no. January, p. 100032, 2021.
[5] G. Hammond and C. Jones, “BSRIA Guide, The Inventory of Carbon and Energy (ICE): Embodied energy and carbon in construction materials,” 2011.
[6] “ÖKOBAUDAT–Sustainable Construction Information Portal.” [Online]. Available: https://www.oekobaudat.de/en.html. [Accessed: 10-Oct-2021].
[7] “EPD Danmark (Environmental Product Declaration).” [Online]. Available: https://www.epddanmark.dk/uk/. [Accessed: 10-Oct-2021].
[8] “EPD-norge (Environmental Product Declaration).” [Online]. Available: https://www.epd-norge.no/. [Accessed: 10-Oct-2021].
To download a .pdf of the Sustainable Insulation brochure, click here.
If you have technical questions on this topic, please email the technical contacts listed on our contact page.
Copyright © 2023 Perlite Institute All Rights Reserved