Lesson 2: The Hydraulic Steering Circuit

In the first article of this series, we looked at the fundamentals of what a fully hydraulic steering system is and the advantages it offers over a traditional power steering or “hydro assist” steering setup. Now let’s look at the components that make up a full hydro steering system and how they work together. For the sake of simplicity, we will only focus on a basic front steering full hydro system. Add-ons like rear steer and hydroboost brakes add complexity and will be covered in future articles.
The most fundamental thing to understand about power steering systems, full hydro or not, is that they form a closed-loop hydraulic circuit. As long as the vehicle’s engine is driving the steering pump, steering fluid is continuously moving through this circuit.
The act of steering a vehicle involves diverting fluid out of this circuit and into a hydraulic cylinder or ram to turn the tires. Since an equal (or almost equal) amount of fluid will be returned from the cylinder at the same time, the main hydraulic circuit maintains a nearly constant volume of fluid in circulation.
Even with “basic” front steering hydro systems, the components and arrangement can vary depending on factors such as the intended use of the vehicle and the type of pump used. However, the major components that make up a typical full hydro steering system include:
- Fluid reservoir
- Steering pump
- Steering control (orbital) valve
- Steering cylinder (ram)
- Filter
- Fluid cooler
Fluid Reservoir
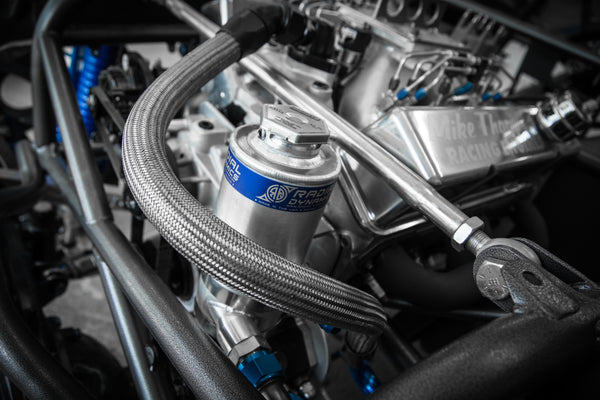
The steering reservoir is like the start/finish line for the hydraulic circuit and is often one of the most overlooked components in a steering system. Most people think of a steering reservoir simply as small tank for holding fluid in the steering system, however, the reservoir also performs several other vital functions that influence the overall performance and reliability of the steering system.
A properly designed reservoir should:
- Hold extra fluid capacity for the steering system
- Provide room for thermal expansion as steering fluid temperature rises
- Separate and remove gas and air bubbles from steering fluid
- Circulate 100% of stored volume to maximize available fluid for energy absorption and heat dissipation
- Provide ideal conditions for supplying fluid to the steering pump in any situation
Especially in off-road applications where extreme operating angles, heat, and fluid sloshing are to be expected, a well-designed reservoir can mean the difference between a trouble-free day on the trails or endless steering problems.
Steering Pump
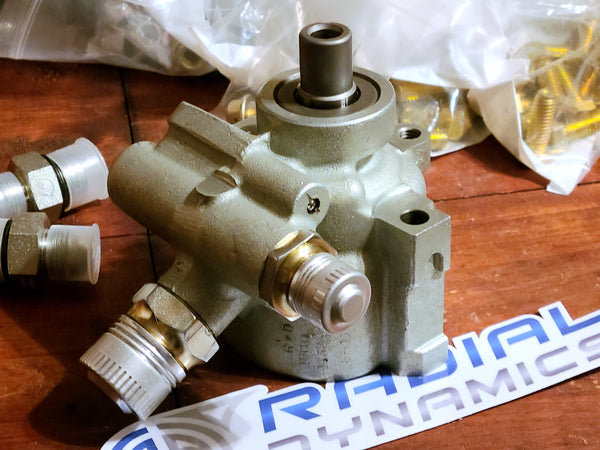
The steering pump is the heart of every steering system. It takes energy from the vehicle’s engine and converts it into fluid power which in turn is used to control the steering position of a vehicle’s axle.
To cover the details of all the various pump types, models, advantages, and disadvantages of each is worthy of its own entire series but in general, all steering and hydraulic pumps operate on the principle of “positive displacement”. This means that pumps will move a certain volume of fluid from their inlet to their outlet with each revolution. As a result, the flow rate of steering fluid moving through the hydraulic circuit is directly related to the pump displacement per revolution, engine speed, and any flow-regulating valving (if present).
What this all boils down to is that steering pumps produce “constant flow” (for a given engine speed) but not “constant pressure”. At rest, the steering system is under relatively low pressure. It is only during the act of steering that system pressure rises since the fluid needs to overcome any resistance to its flow path such as big heavy tires pushing back on the steering cylinder.
For off-road steering systems, flow rates can easily range from 3 up to 16 gallons per minute (GPM) and operate at maximum pressures in the range of 1200 PSI to 2000 PSI.
Steering Control (Orbital) Valve

If the pump is the heart of a full hydro steering system, then the steering control valve could be considered the brain.
The function of the steering control valve is to divert fluid from the main hydraulic circuit into the steering cylinder to maintain desired steering position. Since the valve meters the volume of fluid in relation to rotation of the steering wheel, the vehicle response feels much like steering a normal car. Larger displacement valves result in fewer turns to steer lock-to-lock but they also demand more flow which is why it is so critical that valves, cylinders, and pumps are sized to properly work together.
Steering control valves are also known by other names including “orbital valves” and “Char-Lynn valves”. While Char-Lynn is simply a brand name, the term “orbital valve”, although not technically accurate, has gained almost universal adoption in the world of off-road motorsports.
Steering Cylinder (Ram)
A steering cylinder, also known as a steering ram, is a device that converts pressurized fluid into mechanical force which is applied between the axle housing and steering arm to adjust steering position. The force produced is directly related to the piston area of the cylinder and the fluid supply pressure. A larger-piston cylinder can produce more force for a given pressure but also requires more fluid volume to achieve a given stroke length.
There are generally three types of steering cylinder configurations:
- Double-ended cylinder
- Single-ended cylinder
- Double single-ended cylinders
Double-ended cylinders have a shaft that extends through both ends of the cylinder. As a result, the force produced is equal in both directions of actuation and the number of turns lock-to-lock is equal from left to right.
Single-ended cylinders have a shaft that extends only through one end of the cylinder. In general, they are more compact and easier to mount than double-ended cylinders but they are unbalanced. During extension, a single-ended cylinder produces more force but also takes more turns to reach lock-to-lock than during retraction. The displacement of the shaft during retraction also causes the fill level in the reservoir to fluctuate when steering.
Double single-ended cylinder arrangements involve using two single-ended cylinders, one connected to each steering arm, with a traditional tie rod ensuring the two cylinders operate in unison. By plumbing both cylinders together, these arrangements can produce extremely high steering forces in reasonably sized packages that are most found in heavy duty applications such as monster trucks.
Filter

Fluid cleanliness is often considered the most important operational property in hydraulic systems and as such, a properly selected fluid filter is one of the most beneficial additions you can make to extend the life of your steering system. Steering pumps and valves have extremely tight internal clearances meaning that even small solid particles present in steering fluid can quickly cause damaging wear.
For safety and product selection reasons, filters are typically located in the low-pressure return side of the steering circuit between the steering control valve and reservoir. Filters should never be located between the reservoir and pump as this can potentially starve the pump and lead to cavitation.
Fluid Cooler

Fully hydraulic steering systems generally operate at higher pressures and flow rates than traditional power steering systems and in the process, end up generating greater amounts of heat.
Steering fluid is the life blood of a steering system that not only transmits energy from the pump to the steering cylinder but also provides vital lubrication and cooling of internal pump and valve components. In order to perform these functions, it is critical to maintain proper fluid viscosity which is strongly affected by temperature.
If fluid temperature gets too high, viscosity can reduce to the point that it shortens the life of the steering system so for vehicles intended to operate for long periods of time or under particularly demanding conditions, a properly sized fluid cooler can go a long way in maintaining ideal fluid properties.
Like with filters, fluid coolers are typically installed in the low-pressure return portion of the steering circuit. While plate or radiator type coolers can be highly effective, oftentimes a well-designed finned tube cooler is plenty adequate for even the most demanding steering applications and easier to package in a tight chassis.
Conclusion
When it comes to steering system design, one cannot evaluate a single component without considering how it will affect every other piece of equipment in the steering circuit. All too often, having just one component under- or over-sized will result in drastic unintended consequences that affect overall steering performance and longevity which is why it is important to understand the fundamentals behind system operation.
If you are having questions about whether a certain product is the right fit for your steering system, consulting an experienced professional like Radial Dynamics can help ensure steering success before wasting hundreds or thousands of dollars on the wrong parts.