The AH-64 Apache: The deadliest US attack helicopter (with the most hazardous… air conditioning system?)
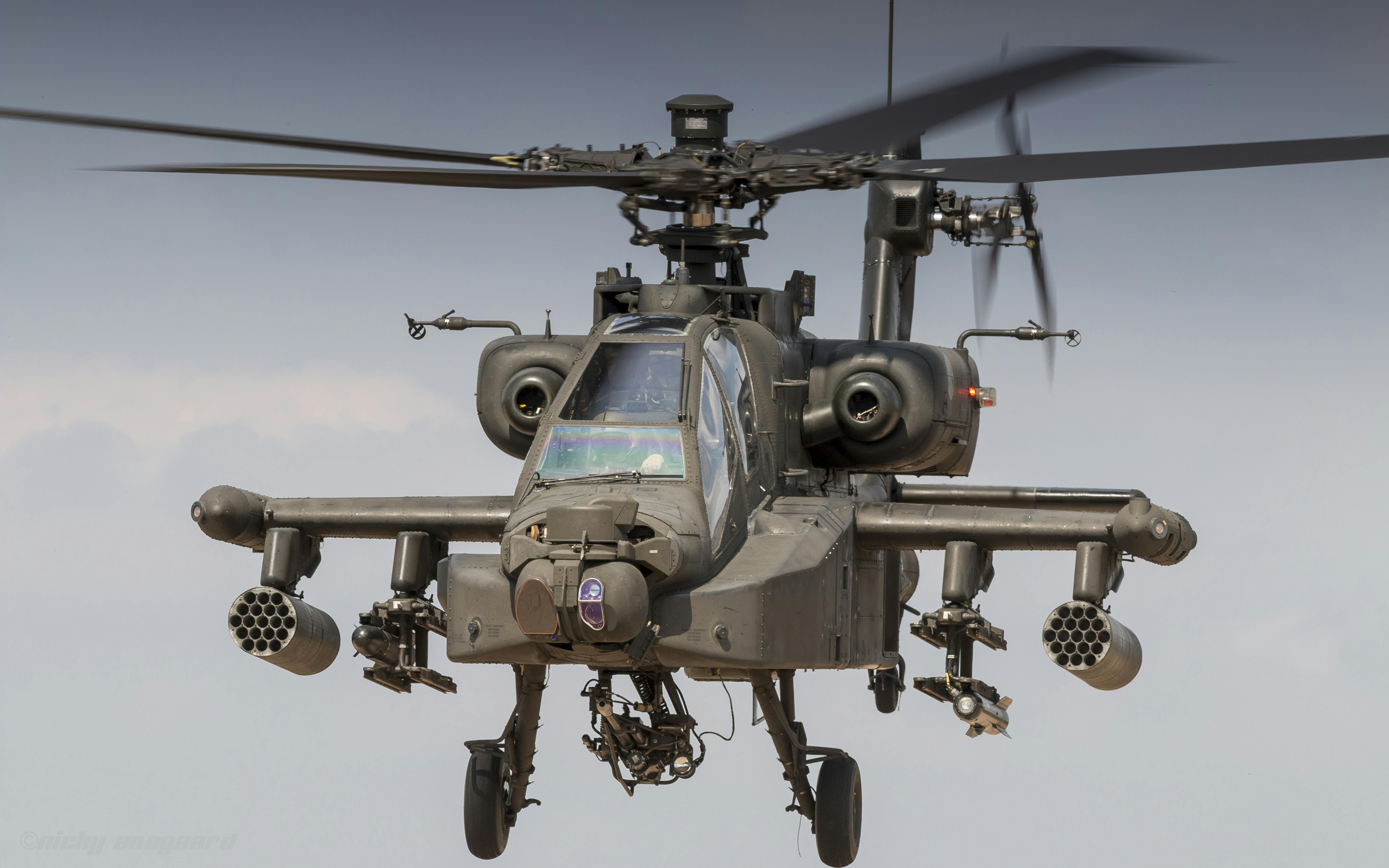
Hollywood has often made stars of machines, intentionally or unintentionally. Baa Baa Black Sheep (renamed Black Sheep Squadron for its second season) made a lot of disco-era TV viewers wish they could fly the F4U Corsair fighter plane. In the ‘80s, Iron Eagle made an entire generation of Gen X’ers want to blow up terrorists while piloting the F-16 Fighting Falcon. Top Gun (released later in 1986 than Iron Eagle, incidentally) refocused teenage airplane fans’ lust on the F-14 Tomcat, with possibly some hormones left over for Tom Cruise and Kelly McGillis. (Automobiles were not excluded… Christine starred its eponymous 1958 Plymouth Fury as a main character.) And most recently, the F/A-18 Super Hornet has received a lot of renewed interest and attention due to Top Gun: Maverick.
Well, ladies and gentlemen, let us introduce you to Fire Birds (1990), a truly, magnificently terrible movie featuring Nicolas Cage (our favorite crappy actor), Tommy Lee Jones (a selectively crappy actor), and Sean Young (an unarguably crappy actor) all chewing up the scenery and doing their best to out-overact each other. And, paradoxically, they all win that contest…. but everyone who watches this movie loses.
However, while Fire Birds is entirely forgettable, its real star, the AH-64 Apache attack helicopter, is not. First entering US Army service in April 1986, the Apache is still the most feared helicopter in the US arsenal, and unlike the movie, the AH-64 has only gotten better with age. Let’s go into the details of this deadly, capable rotary-winged attack aircraft.
A brief history of the AH-64 Apache
In the early 1970s, the US Army was searching for an advanced anti-armor aircraft to bolster its capabilities, similar to the Air Force’s A-10 Thunderbolt II and the Marines’ Harrier V/STOL attack fighter. (The initial concept was for a multi-role helicopter; however the final design skewed into the attack helicopter role, with a specialization in defeating armored targets.) Problem: Since 1948, the Joint Chiefs and the branches of the military have agreed that the Army should be restricted against developing fixed-wing aircraft, so a helicopter or other rotary-wing design was necessary. The Army had the AH-1 Cobra, which it deployed with success in Vietnam, but was seeking something with increased firepower, range, ceiling, and anti-armor capabilities.
So, in November 1972, the Army released a Request For Proposals (RFP) for the Advanced Attack Helicopter (AAH) program, and prioritized it as one of its five main projects the next year. Initial proposals were submitted by Bell, a combined Boeing Vertol/Grumman team, Hughes, Lockheed, and Sikorsky. In July 1973, the Department of Defense selected Hughes and Bell as the finalists, and both companies were given a contract to build a prototype.
By the autumn of 1975, both Hughes and Bell had completed flying prototypes. Hughes’ was called the Model 77 (the Army gave it the designator YAH-64A) and Bell’s was the Model 409 (YAH-63A). After flight tests and further evaluations, the Army chose Hughes’ design as the winner, citing its durable and efficient 4-blade main rotor and more stable “taildragger” landing gear arrangement.
Hughes was then contracted to build 3 pre-production aircraft, which were evaluated for weapons system compatibility, and modified to fire the new Hellfire anti-tank missile (Helicopter Launched, Fire and Forget, given the acronym HELLFIRE because it sounds more bitchin’), which had been in development since 1974.
In 1981, the three pre-production AH-64As were handed over to the Army for additional operational testing, which was deemed a success, but as a result of feedback from evaluators, the engines were upgraded to more powerful General Electric T700-701 turboshaft engines, originally rated at 1,690 shaft horsepower (shp). (A turboshaft is a jet turbine engine that drives an output shaft connected to a transmission, rather than driving a turbofan as in a typical jet transport airplane.)
The AH-64 was officially given the name Apache in late 1981, following the Army tradition of naming helicopters after Native American tribes or leaders. (It’s intended to be a compliment, we promise.) The Apache was approved for full-scale production in 1982, and the first production AH-64 rolled off the line at the Hughes Helicopter (later McDonnell Douglas, later Boeing) facility in Mesa, Arizona in 1983.
After more testing and tweaking, the Apache entered US Army service in April 1986, and has served in pretty much every conflict since. The Apache is in use by multiple US allies, including Egypt, Greece, India, Indonesia, Israel, Japan, Korea, Kuwait, Morocco, the Netherlands, Qatar, Saudi Arabia, Singapore, Taiwan, United Arab Emirates, and the United Kingdom.
The steel-composite rotors fitted to the first models of the Apache proved not to be as durable as predicted, and needed replacement after only 146 flight hours, far less than the Army’s specification of 1,500 flight hours. However, as with other systems on the aircraft, the rotor blades have been continually improved, and rotor blade life was extended to a more satisfactory 1,400 hours by early 1991.
How much does an AH-64 Apache helicopter cost and how many have been built?
In 1986, the incremental or flyaway cost for the AH-64A was cited as $7 million per copy ($19.8 million in today’s Monopoly money), and the average unit cost was approximately $13.9 million ($39.2 million today). However, several sources state the current unit cost of the latest AH-64E Apache as $52 million. That’s more than twice the production budget of Fire Birds ($22 million)… and for our money, the AH-64E is more than twice as enjoyable to watch.
Over 2,400 Apaches have been built since 1983. Active contracts plan for AH-64E production until 2028, with a current acquisition objective of 812 total aircraft of the latest type.
What are the dimensions and main performance characteristics of the AH-64 Apache?
The Apache’s fuselage is 58 feet 3 inches (17.76 meters) long. The current model is 15 feet 3 inches high (4.64 meters) to the top of the radar dome, and has a 48 foot main rotor diameter (14.63 meters). It has a ready to fly weight of 17,650 lbs (8,000 kg), and a maximum takeoff weight of 23,000 lbs (10,433 kg), but sources vary there. The Army’s Acquisition Support Center says the maximum gross weight is 20,260 lbs.
As mentioned earlier, Apaches use two General Electric T700-701 turboshaft engines initially putting out 1,690 shp, increasing with improvements over the years to around 1,890 shp for the 701C variant, and currently the T700-701D engines being fitted to the most recent AH-64E model produce 2,000 shp each. Maximum speed of the AH-64A was 172 mph (276 kph) in level flight, while the latest AH-64E’s maximum speed is 188.7 mph (303 kph). Cruising speed is 165 mph (265 kph), and maximum ferry range (unarmed, extra fuel tanks) is 1,178 miles (1,896 km)
The Apache’s combat range is 260 nautical miles (about 300 miles or 481 kilometers). With a full combat load, a fully fueled Apache can remain airborne and on station for 2.5 hours.
The Apache’s standard rate of climb varies between 1,595 feet per minute (486 m/min) and 1,775 fpm (541 m/min), depending on air temperature and density. (Hotter air=less density=reduced performance). Its service ceiling similarly varies between 19,400 feet (5,900 m) and 21,000 feet (6,400 m), depending on how hot the ambient temperature is.
A useful feature of the AH-64 is its folding, 4-bladed, composite main propeller, which allows Apaches to be loaded and transported in a C-17 Globemaster, C-5 Galaxy or other military transport aircraft, without the need for disassembly of the helicopter for transport.
AH-64 Apache armament and warfare systems
The Apache was intended from the start to be an advanced, anti-armor attack helicopter, and it has only been improved over its decades of service. Current Apaches have advanced avionics and electronic systems, including battle integration software that increases the internet/intranet capability of all players on the modern battlefield. The newer AH-64s also have an automated stability augmentation system, and a digital autopilot system that can partially or fully take control of the Apache in flight, so the pilot or gunner can focus on problems or threats without having to worry about controlling the aircraft. Like many other US military aircraft, the Apache also features a passive infrared countermeasure system that automatically deploys flares if it detects an incoming missile.
In addition to carrying up to 16 of the aforementioned Hellfire missiles, which is an anti-armor missile that can be either laser-guided or radio-frequency (radar) guided, depending on battlefield requirements, the Apache can carry two pods of 19 Hydra rockets each, for anti-aircraft or ground attack.
But by far the most famous and impressive bit of weaponry on the Apache is its M230 electrically cycled, 30 millimeter chain gun (or auto-cannon). The gun is capable of firing up to 650 rounds per minute of high-explosive incendiary or armor-piercing rounds, but in practical use, a 300-rpm rate of fire with a significant cooldown between engagements is needed, since the cannon uses only one barrel and is air-cooled (unlike multi-barreled rotary cannon such as the Phalanx CIWS).
One of the revolutionary features of the Apache is its helmet mounted targeting display, the Integrated Helmet and Display Sighting System (IHADSS). Apache crews consist of a pilot (in the rear seat) and a co-pilot/gunner (CPG) in the forward seat. Both crew members are certified to fly the Apache, and there are redundant controls in both crew positions. Additionally, using the IHADSS, either the pilot or the CPG can slave the hydraulically actuated M230 cannon to their helmet’s movements, so the cannon automatically tracks their head movements, targeting whatever the pilot/gunner looks at through his/her helmet eyepiece reticle. This has proven extremely effective in a combat environment, in addition to being absolutely badass, even when used by Nicolas Cage.
The Apache Longbow’s radar and targeting capability is a game-changer (plus AH-64E upgrades)
Starting in the 1980s, new breakthroughs in radar technology allowed the development of the system eventually termed the AN/APG-78 Longbow, which is the millimeter-wave fire-control radar (FCR) system used on the AH-64D Longbow and AH-64E Apache variants.
This compact, flattened radar dome sits atop the main rotor, which gives modern Apache crew the ability to see over obstacles, buildings, trees, and terrain better than nose-mounted radar systems.
The radar allows advanced terrain-following capability, so Apaches can safely fly at very low altitudes, even in bad weather or at night. This helps avoid detection by enemy radar or visual observation, and enhances the Army’s ability to penetrate enemy defensive networks and effectively strike targets without warning.
The Longbow radar is capable of tracking up to 128 hostile targets at once, and the system can engage up to 16 simultaneously. It’s unclear whether this limitation is due to the Apache’s full loadout of 16 Hellfire missiles, or whether this is a restriction related to the software/hardware of the radar, but we suspect the former, as the number is too convenient. The integrated radio internet system incorporated into the Apache’s sensor suite also allows the data from one helicopter to be shared among ground units and other aircraft, allowing multiple teams and aircraft to fire at targets detected by a single Apache.
A key feature of the Apache’s deadly effectiveness, and its ability to strike multiple targets at once, is the Longbow’s available “fire and forget” mode. Using this option, the targeting radar can identify and track a target, and then guide a missile to it, without requiring the pilot to maintain a continuous lock.
Additionally, using the Longbow system, targets that are beyond the line of sight of the pilot can also be effectively targeted and engaged. This greatly increases the battlefield capability of the Apache.
The AH-64E or “Echo” variant, (formerly known as the AH-64D Block III) features upgraded T700-GE-701D engines with 2,000 shaft horsepower each, and an improved transmission to handle the increased power. This enables the Echo to fly higher and faster.
The latest Apache is also getting an upgraded radar system with extended range, and utilizes a modern, open-systems architecture that can incorporate the latest communications, navigation, sensor, and weapons systems. The Echo gets multiple upgrades to its combat electronics, including an improved Modernized Target Acquisition Designation Sight/Pilot Night Vision System (MTADS/PNVS), incorporating a new FLIR (Forward-Looking Infrared) system. The MTADS/PNVS system includes a new integrated infrared laser that allows for easier target designation and enhanced infrared imagery that combines infrared and night vision capabilities for improved pilot/gunner visibility and target identification.
The Army says the AH-64E “is also undergoing further modernization modifications such as the Modernized Day Sensor Assembly. This upgrade eliminates obsolescence issues while enhancing day-sight capabilities equivalent to the changes made with MTADS/PNVS. Other modifications include Manned-Unmanned Teaming that provides non-line-of-sight communications, video transmission/reception, and maintenance cost reductions.”
So, what about this ostensibly hazardous air-conditioning system?
Does the Apache helicopter have an air conditioning / environmental control system (ECS)?
Yes, it does! All AH-64 Apaches have two redundant air conditioning or Environmental Control System (ECS) modules, located at the rear of each fuselage extension (where it swells out along the bottom). The intakes face the rear of the aircraft and the ECS exhaust ports are on the side, just around the “corner,” forward of the intakes.
The first iterations of the AH-64 used a basic, shaft-driven compressor cooling system, which was adequate for the first few years of use (when it worked; more on this below) but was deemed insufficient once the improved “Longbow” Apache configuration was developed.
In November 1991 the United States General Accounting Office (GAO) report to Congress detailed the planned upgrades to the AH-64 airframe, including expanded forward avionics bays to accommodate Longbow radar targeting/weapons equipment, upgraded generators, batteries, and transformers for additional electric power, as well as an upgraded processing system. All of these systems generated a significant amount of additional heat, so the report specified the need for an upgraded “vapor cycle cooling system to replace the often troublesome shaft-driven compressor cooling system.” Ah, the delicious problems of modern aerospace environmental control systems!
In 1997, Fairchild was awarded a piece of McDonnell Douglas Helicopter Systems’ $73 million contract to provide the improved ECS for the upgraded Longbow Apaches, which comprises “a distributed vapour-cycle cooling and heating unit consisting of two redundant systems with dual-speed compressors, 1553 digital-databus controllers and multiple heat-exchangers, fans and control valves. The system has Fairchild Heli-Rotor 54mm compressors and environmentally friendly refrigerant for cooling of avionics and crew, and controls engine bleed-air for crew heating.”
In very simple terms, this type of system operates in a closed loop, in which the refrigerant, driven by a compressor, absorbs heat from the cabin and sheds it, typically assisted by axial fans, into the outside air. The refrigerant then returns in a loop to the cabin to repeat the cycle.
The Apache air crew members we’ve consulted have all commented on the effectiveness of the updated air-conditioning system, some referring to it as capable of “producing snowflakes” or even building up ice on some surfaces in the crew compartment under certain circumstances. Since the Apache was designed to operate in “hot and high” environments as well as steamy jungles and everywhere else, its ECS system has to be top notch. The greenhouse effect of a glass or plexiglass-lined helicopter cockpit sitting on the blistering tarmac in Iraq can quickly raise the internal temps above 150 degrees if the ECS isn’t working properly.
However, although the Apache’s ECS is effective at keeping its crew and avionics frosty even in the punishing heat of the Middle East, the designers of the ECS weren’t concerned about excessive noise, and focused on maximizing efficiency, compactness, and lightness, all key attributes of any Intergalactic thermal systems technology.
As a result, the Apache’s system is extremely loud. You may not think this would create any problems, particularly with twin turboshaft engines and a 48-foot-diameter, 4-bladed composite main rotor chopping away above, but as we will see next, it can create a hazardous condition in some situations.
The Apache’s ECS is so loud it can be harmful to maintenance crews
In 1997, Boeing acquired/merged with McDonnell Douglas, including MD’s Apache helicopter-maintenance duties. At Boeing’s Mesa, Arizona facility, where the Apache’s maintenance and upgrades are performed, the Apache’s ECS must be operated whenever the aircraft’s powerful avionics and electronics systems are on, because they generate a significant amount of heat.
Unfortunately, as noted above, the Apache’s very effective air-conditioning system is loud, exceeding 106 decibels, well over the 85 dB limit above which prolonged exposure can cause permanent hearing damage. (Audiologists actually often recommend ear protection for any prolonged noise above 70 dB. OSHA’s permissible exposure limit is 90 dB for all workers for an 8-hour day.) As a comparison, lawnmowers and loud power tools produce around 90 dB at the source, and nightclubs, gas-powered leaf blowers, and car horns usually start around 105 dB.
This means that Apache ground and maintenance crew members, particularly those working indoors while undergoing the testing phase of the Apache’s electronic systems (which can last for up to 8 hours), are subjected to potentially harmful noise levels while in proximity to the running ECS intake and exhaust ports, or even from across the room. That’s right… The Apache is so deadly that even its air-conditioning system is potentially harmful to humans. What!? The noise also makes having a conversation in the same room or troubleshooting between maintenance teams difficult.
The racket got so bothersome that Jason DeStories from Boeing Research & Technology and his teammates at Boeing’s Mesa, AZ Apache facility designed and built an award-winning, cost-effective sound-deadening system, repurposing aluminum sheeting, scraps of shipping foam, and PVC pipe tied together with zip ties. ‘Merica!
DeStories says, “We call it a ‘hush kit.’ The foam absorbs the high-frequency noises. The baffling eliminates a direct line of sight and sound. This forces all sound energy through the foam and deflects noises internally to maximize the chance of absorption. When we measure sound at the source at the inlets, for example, the hush kits reduce noise by 75%.”
The team’s lightweight, mobile hush kits are easily moved into place against the intake and exhaust ports of the ECS on both sides of the Apache when teams are working indoors, and make it a lot more pleasant to work around. Intake noise is reduced from 100 to 88 dB, and exhaust noise is reduced from 106 to 96 dB.
It’s important to understand that measuring noise by decibels uses a logarithmic scale, not a linear one. For every 6 dB reduction, the actual noise is cut in half.
Perhaps a similar technique could be employed to hush the loud and, potentially hazardous noises coming out of the mouths of Nicolas Cage and Sean Young. (We love you, Nic.)
–By Jeff Davis, Intergalactic Scribe
Sources:
https://asc.army.mil/web/portfolio-item/apache-attack-helicopter-ah-64d-e/
https://helicoptermaintenancemagazine.com/article/helicopter-vapor-cycle-air-conditioning-system
https://www.flightglobal.com/fairchild-cools-down-longbow-apache/1202.article
https://en.wikipedia.org/wiki/Boeing_AH-64_Apache
https://youtu.be/PD-dTFTYOuQ?si=zdat-97cw0Jmd5tx
https://www.boeing.com/features/innovation-quarterly/2021/10/sound-check.page#