Linear Actuators: Transforming Motion Control in Various Industries
Are you ready to dive into the exciting world of motion control? Look no further, because this blog post is here to introduce you to a game-changing technology: linear actuators. From aerospace engineering to healthcare and everything in between, these versatile devices are revolutionizing the way we move and manipulate objects. Whether you’re a tech enthusiast or simply curious about how these tiny yet powerful gadgets work, get ready for an exhilarating journey as we explore how linear actuators are transforming industries across the board. Buckle up and let’s embark on this thrilling ride together!
Introduction to Linear Actuators
Linear actuators are devices that create linear motion using a variety of methods, including hydraulic, pneumatic, and electrical. These devices are used extensively in industries such as automotive, aerospace, and manufacturing.
Hydraulic linear actuators use fluid pressure to create linear motion. Pneumatic linear actuators use compressed air to create linear motion. Electrical linear actuators use an electric motor to create linear motion.
Linear actuators are used extensively in industries such as automotive, aerospace, and manufacturing. In the automotive industry, they are used for opening and closing car doors, adjusting seats, and controlling windows. In the aerospace industry, they are used for moving aircraft control surfaces and operating landing gear. In manufacturing, they are used for moving heavy loads and positioning materials during assembly processes.
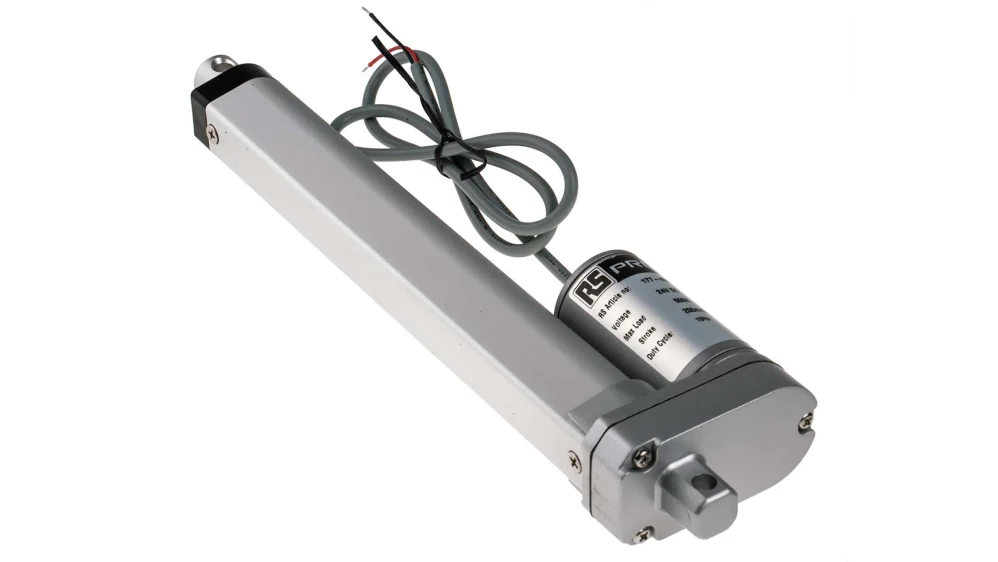

Types of Linear Actuators
There are three main types of linear actuators: pneumatic, hydraulic, and electric. Each type has its own advantages and disadvantages that make it more or less suitable for different applications.
Pneumatic linear actuators use compressed air to generate force. They are typically smaller and lighter than hydraulic or electric actuators, and can be used in environments where flammable liquids are present. However, they require a reliable source of compressed air, which can be expensive to maintain.
Hydraulic linear actuators use oil or water as the working fluid. They are more powerful than pneumatic actuators and can operate in very high temperatures. However, they are also much larger and heavier, making them less suitable for portable applications. In addition, hydraulic fluids can be messy and difficult to clean up if they leak.
Electric linear actuators use an electric motor to generate force. They are often smaller and lighter than hydraulic actuators, but can still provide a very high level of force. Electric actuators also have the advantage of being able to operate in both high and low temperatures. However, they require a power source, which may not be available in some industrial applications.
The type of linear actuator you choose will depend on your application and budget. Each type has its own advantages and disadvantages, so it is important to consider all of the factors before making a final decision.
Applications of Linear Actuators in Different Industries
Applications of Linear Actuators in Different Industries
Linear actuators are devices that produce linear motion using a variety of methods including hydraulics, pneumatics, and electromechanics. These devices have a wide range of applications in different industries, and they are constantly being used to create new products and improve existing ones. Here are some of the ways linear actuators are being used in different industries:
In the automotive industry, linear actuators are used in car seats to adjust the height and angle of the seat. They are also used in electric windows to open and close them. In the aerospace industry, linear actuators are used in aircraft flight control systems. They are also used in satellite deployment systems and space station docking mechanisms. In the construction industry, linear actuators are used in cranes and lifting equipment. They are also used in door openers and automatic doors. In the food and beverage industry, linear actuators are used in packaging and labeling machines. They are also used in conveyor belts to move food products from one location to another.
Linear actuators have a wide range of applications in many different industries. Their versatility and reliability make them an invaluable tool for engineers who are looking to create new products or improve existing ones.
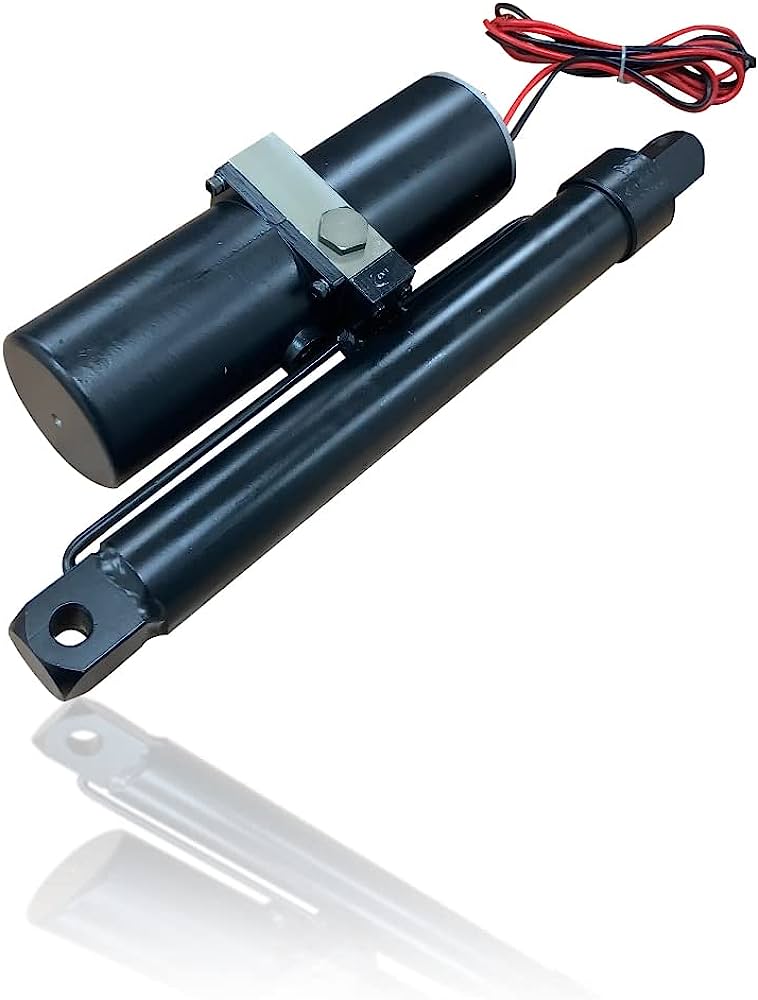
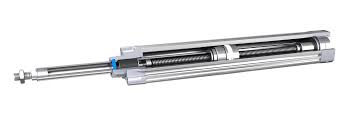
Advantages of Using Linear Actuators
Linear actuators are used in a wide variety of industries to provide precise and efficient motion control. There are many advantages to using linear actuators over traditional methods of motion control, such as hydraulic cylinders or pneumatic cylinders.
Some of the advantages of using linear actuators include:
Precision: Linear actuators can provide very precise and repeatable motion, which is essential in many applications such as semiconductor manufacturing or medical equipment.
Efficiency: Linear actuators are much more efficient than traditional methods such as hydraulic cylinders, which can waste a lot of energy through heat loss.
Safety: Linear actuators are much safer than traditional methods, as they do not rely on high pressure fluids or gases which could leak and cause injury.
Environmentally friendly: Linear actuators do not use hydraulic fluids or gases, which can be harmful to the environment. They are also often made from recycled materials.
Cost effective: Linear actuators are typically more cost effective than traditional methods, due to their efficiency and lack of required maintenance.
Versatility: Linear actuators can be used in a variety of applications, from automotive to industrial. They are also relatively easy to install and maintain.
How Do Linear Actuators Work?
A linear actuator is a mechanical device that creates motion in a straight line. It is often used as an alternative to traditional hydraulic or pneumatic cylinders, which can be more expensive and difficult to maintain. Linear actuators can be powered by electricity, compressed air, or hydraulics.
When an electric linear actuator receives power, it creates a magnetic field around the rod inside the housing. This magnetic field interacts with the rod, causing it to move. The amount of force generated by the actuator depends on the strength of the magnetic field and the length of the stroke (the distance the rod can travel).
Compressed air-powered linear actuators work similarly to electric ones, but use compressed air instead of electricity to create the magnetic field. Hydraulic linear actuators use fluid pressure to generate force. They are typically used for heavy-duty applications where high levels of force are required.
No matter which type of linear actuator is used, the resulting motion is usually converted into rotary motion through a crank or cam as necessary. Linear actuators are widely used in industrial automation and robotics applications, automotive systems, and medical devices.
A linear actuator works by converting energy into a linear motion which can be used to move or control an object. Linear actuators come in many shapes and sizes and they can be powered by electricity, compressed air, or hydraulics. Depending on the application, the force generated by the actuator is controlled using a magnetic field, fluid pressure, or other means of generating power. The resulting motion is then converted into a rotary motion as required. Linear actuators are versatile tools used in many industries for a variety of applications.
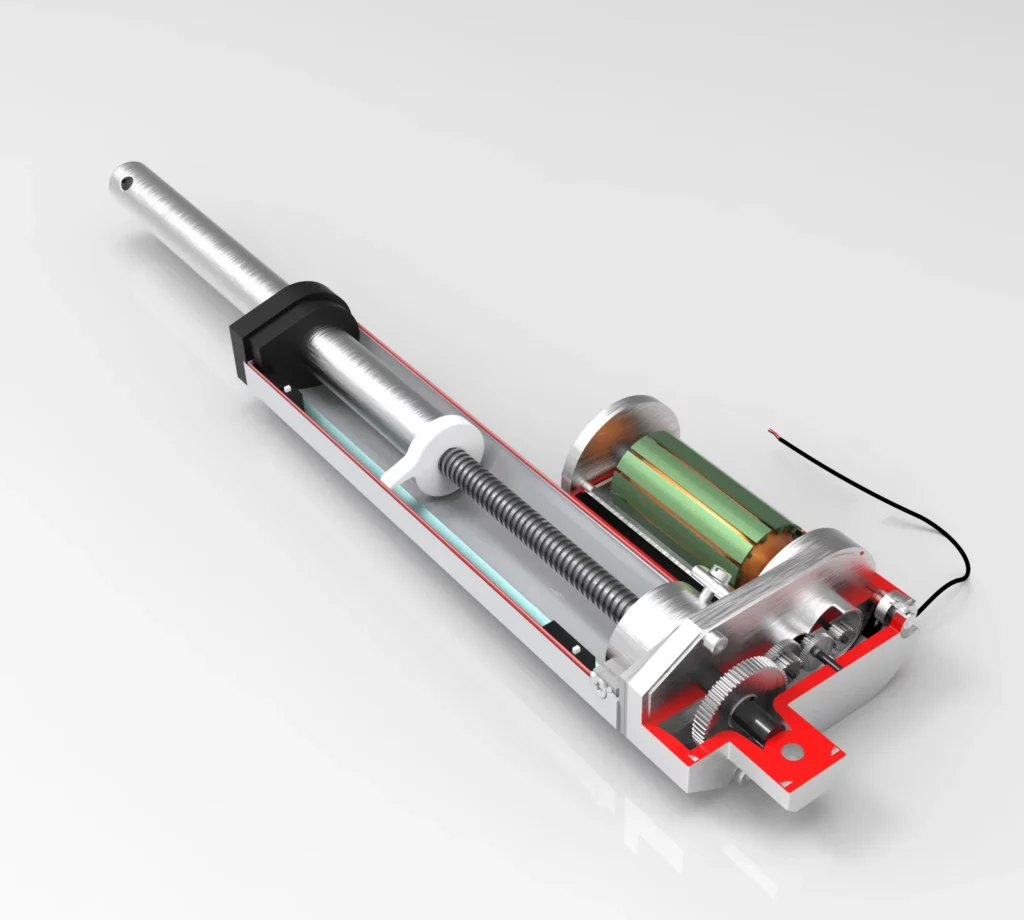
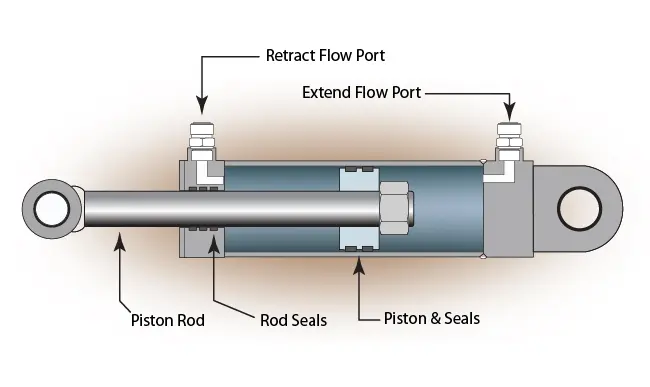
Maintenance Tips for Linear Actuators
As with any machinery, regular maintenance is necessary to keep linear actuators running properly. Here are some tips on how to maintain your linear actuators:
-Inspect the actuator regularly for any damage or wear and tear.
-Lubricate the moving parts of the actuator with a suitable lubricant.
-Keep the actuator free of dirt, dust and other debris.
-Make sure that the power supply to the actuator is functioning properly.
-If any part of the actuator needs to be replaced, only use genuine replacement parts from the manufacturer.
-Check the electrical connections regularly and make sure they are secure and properly insulated.
-Keep the environment around the actuator clean and free of obstructions.
-Make sure that all safety devices are working properly before operating the actuator.
-Regularly test the performance of the actuator to ensure it is operating at peak efficiency.
Following these tips will help to ensure the longevity and proper functioning of your linear actuator.
Conclusion
Linear actuators have revolutionized the motion control industry, providing precise and reliable control for a variety of applications. For users looking to reduce costs or increase efficiency, linear actuators are an excellent choice. With their easy installation and simple operation, they provide a powerful solution that can be used in virtually any application where precision is required. Whether you’re automating industrial processes or controlling delicate medical equipment, linear actuators provide the perfect solution.
Our Products
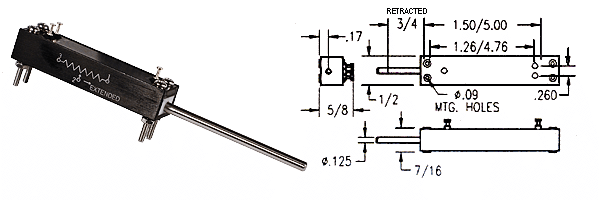
Conductive Plastic Element Black Anodized Aluminum Body, Stainless Steel Shaft, Gold Plated Terminals Recommended for Test and Lab Equipment, Industrial Applications, Medical Equipment (non-life support) Life Expectancy: 20 million strokes Resistance Tolerance: 20% standard (10% Available) Linearity Tolerance: .5% to 1.5% standard (0.3% to 1.0% Available) Power Rating: 0.2 to 1.2 Watt Electrical Stroke: 1″ […]
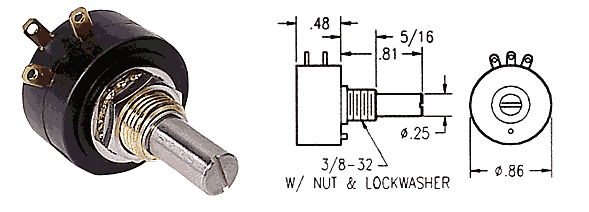
Conductive Plastic Element. Gold Plated Terminals. High Temp. Thermoplastic Housing. Stainless Steel Shaft. Recommended for Medical Equipment (non-life support), Robotics, Industrial, Test and Lab Equipment. Life Expectancy: 10 million turns Resistance Tolerance: ± 10% standard ( ± 10% available) Linearity Tolerance: ± 1.0% standard ( ± 0.5% available) Electrical Angle: 320º ± 5º Mechanical Angle: […]
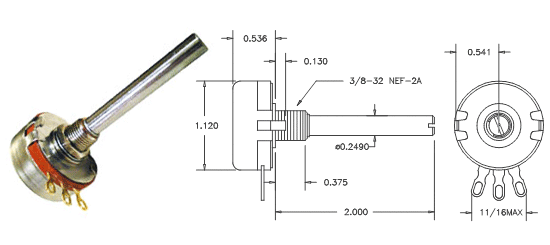
Hot molded carbon element Gold-plated terminals Stainless-steel shaft and housing Quality meeting or exceeding MIL-R-94 – QPL listed Rotational Life: 25,000 Resistance Tolerance: ± 10% or ± 20% Operating Temperature Range: -65°C to +125°C Power rating: 2 watts Insulation Resistance – dry: 10K Meg; wet: 100K Meg Dielectric Strength: 900 VRMS Starting Torque: 1 oz/in […]
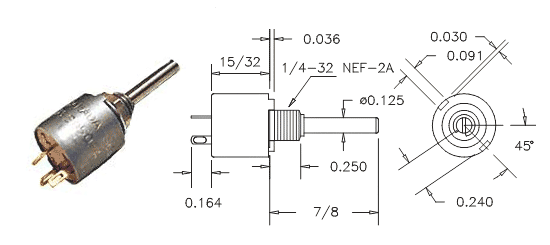
Hot molded carbon element One piece housing and bushing Stainless-steel shaft Quality meeting or exceeding MIL-R-94 – QPL listed Rotational Life: 25,000 Resistance Tolerance: ± 10% or ± 20% Operating Temperature Range: -65°C to +125°C Power rating: 0.5 watts Insulation Resistance – dry: 10K Meg; wet: 100K Meg Dielectric Strength: 750 VRMS Operating Torque: 0.5 […]
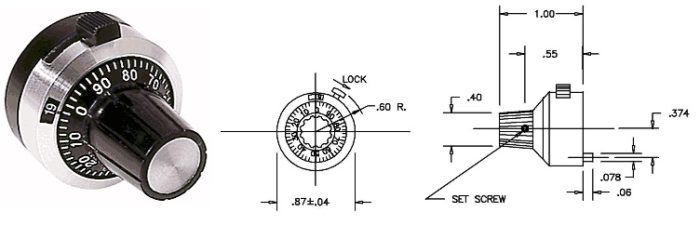
MG22 Concentric Turns Counting Dial Counts up to 20 turns. One Piece Mounting. Aluminum Housing. Black Nylon Knob. Numbers are White on Black Background. Over the Center Lock Available. Diameter – 7/8″; Extension from Panel – 1.0″ Maximum Panel Thickness – 1/4″ Weight: .2 oz
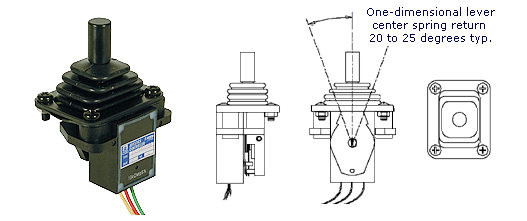
Electrical Specifications: 10K ohm precision potentiometer Single axis joystick Cylindrical knob Linearity (independent): ± 5.0% Lever Electrical Angle: 40° Max. Resolution: Essentially Infinite Mechanical Specifications: ± 20° from center deflection angle Life expectancy: 5 million operations Spring return to center Housing material: High temp. thermoplastic IP65 Rating
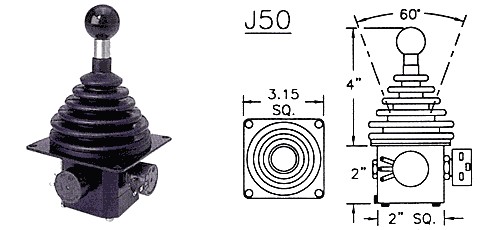
Two axis joystick 4″ handle height 60° deflection angle ( ± 30°) Ball knob Spring return to center Circular deflection pattern 10K ohm precision potentiometer Protective rubber boot (IP54 rating above panel) IP65 option available upon special request Panel mounting bracket
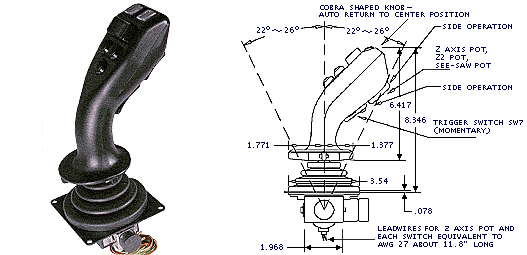
Multi-axis joystick 8.34″ handle height 45° deflection angle ( ± 22.5°) Spring return to center Cobra Head handle Circular deflection pattern 10K ohm precision potentiometers – all axis Three momentary switches (two illuminated, one trigger) Panel mounting bracket Protective rubber boot (IP65 rating above panel)
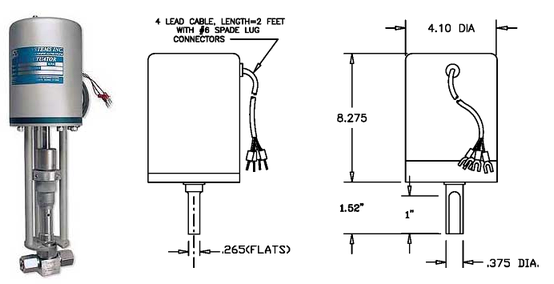
Input: 4 to 20 mA (200 ohms) or 0 to 10VDC (18KΩ) Rotation Speed : 1.5, 3, 5, 10, 20 or 40 RPM Power : 24 VDC (50 Watts min.) Dynamic Braking : Installed Limit Switches : Installed Torque Limiter : Set for Valve requirements. Wt : Approx. 21 in/lbs. max. Seating Limiter : Set […]
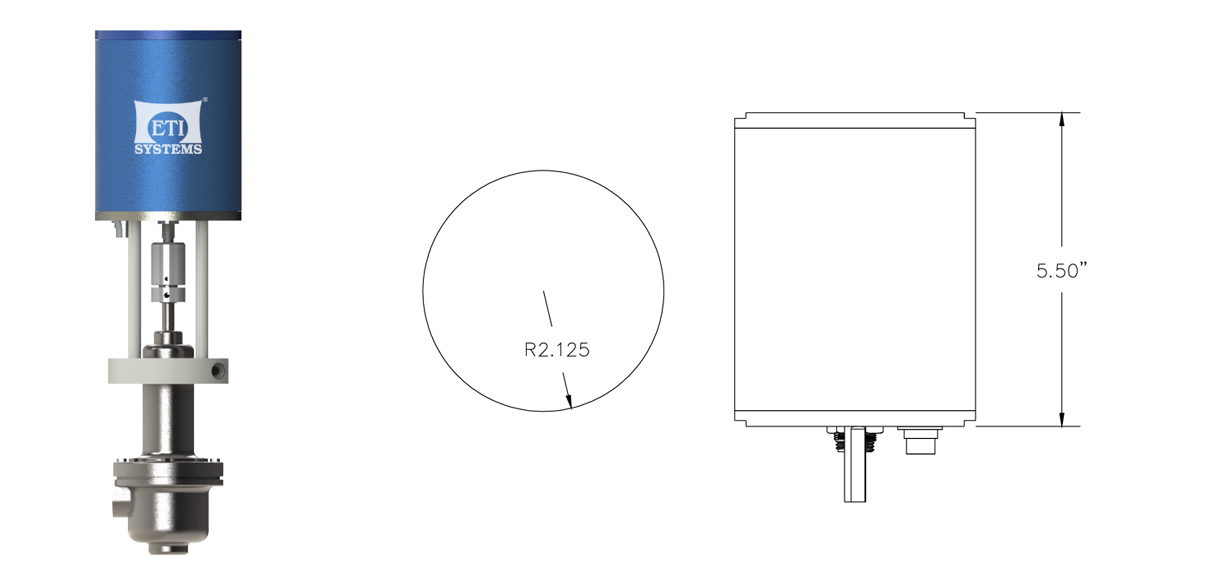