The trend of living in houses made with shipping containers
The demand for this type of housing is growing, due to their affordable prices and their short assembly times. But some still associate them with a lack of comfort
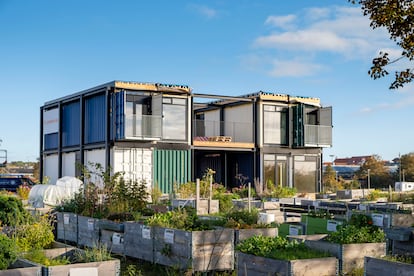
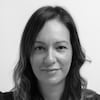
Stadium 974, in Doha, Qatar, designed by the Spanish studio Fenwick Iribarren Architects for last year’s World Cup, was built using standard shipping containers and modular steel elements. Eight years ago, Amsterdam was home to the largest shipping container neighborhood in the world, Keetwonen. The United States is one of the pioneering countries in the construction of houses with these units, particularly in urban areas where there is an urgent need for affordable housing. Australia and the United Kingdom, among others, have also embraced this construction method, which is cheaper and much faster than the traditional one; it has been tested for years in different countries and it is in tune with the global trend to increase the use of recycled materials and promote a circular economy.
This practice has also reached Spain, although it is still new there, and some view it with suspicion. “Demand has increased exponentially since the Covid-19 crisis, but it is still not associated with a feeling of comfort,” says Juan Pedro Fuentes, director of J&J Containers, a Spanish company specialized in the transformation of containers. One of the projects they are building is for a woman with mobility problems. “She has difficulty climbing stairs every day, so she sold her house and we are building her a 90-square-meter [970-square-foot] house with three containers,” says Fuentes.
In addition to people looking for affordable houses, this resource has been employed in Spain as a solution for families in vulnerable situations. The city of Barcelona was the pioneer in the construction of houses made out of containers: it already has two temporary accommodation buildings. Its example was later followed by the island of La Palma, which used it as a way to deal with the emergency caused by the eruption of its volcano in 2021.
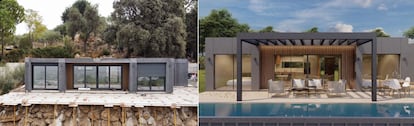
The prices vary depending on the materials used, but it is around €1,350 ($1,500) per square meter. However, “from €800 ($885) per meter you can already get high quality materials,” says Miguel Ángel Rojas, a sales technician for Mundo Contenedor, a Spanish company that has built close to a hundred homes of this kind. The houses are ready to furnish and the bathrooms are included. Another advantage is the building time, which is three to five months.
Developers and investors are beginning to see the formula as a viable business. “We are studying with a Spanish investor to develop 100 three-story container apartments in Motril (Granada) with the aim of renting them out,” says Rojas. Tourist rentals are gaining relevance among the orders received by container recycling companies. “They are projects to assemble four or five houses in independent containers and rent them out. We have requests in Madrid and in Portugal, but they are still dealing with the issue of permits,” says Fuentes.
The companies buy containers that are no longer suitable for maritime transport, but whose structure is in good condition, from large shipping companies. “We use them to give them a second life and convert them into homes, or to do any other modification,” says Fuentes. They can become beach bars, gyms, swimming pools, food trucks... They are made of Corten steel, which is resistant to corrosion and oxidation. For homes, they usually choose refrigerated shipping containers, because they offer thermal insulation thanks to their polyurethane panels, which helps them to maintain a controlled temperature. The cost of these second-hand units, prepared to withstand extreme temperatures, is €1,900 ($2,100); if they are refrigerated, they can go up to €3,500 ($3,900). There are private buyers with DIY skills who directly purchase these containers and do the work themselves, although the companies warn of an increase in scams in online sales.
There are two standard sizes. The 6-meter (20-foot) long containers have a space of 15 square meters (161 square feet), and the 12-meter (40-foot) long ones have 30 square meters (323 square feet). The width is 2.44 meters (8 feet) and “they have a special height of 2.90 meters (9.5 feet) so that when they are isolated they comply with the regulations,” says Fuentes. However, the design is not limited to these two sizes, as the units can be joined, separated or stacked, to create original designs.
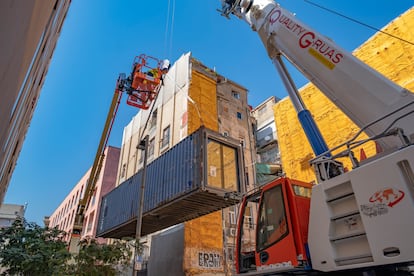
The secret to turning these units into comfortable homes lies in their insulation; that is why it is important to find an experienced professional who can prevent the house from becoming an oven in the summer and a refrigerator in the winter. “We use extruded polystyrene and rock wool in abundance to give it good thermal and acoustic insulation. We also create a 50-centimeter (20-inch) chamber for air circulation on the top and install sandwich panels,” explains Fuentes.
Renewable energy
It is not uncommon for the owners of this type of construction to choose to incorporate renewable energies, such as solar panels or wind turbines, as well as systems for the collection and filtration of rainwater and wastewater treatment equipment. Air conditioning is installed in all the homes, and the most common heating systems are electricity, aerothermics, gas and biomass. “I’d dare to say that it has nothing to envy to a traditional home, as long as the manufacturing is done right,” says Fuentes. On the outside, the containers can be covered with any material, like wood, brick cladding or stone, or they can simply retain their industrial appearance.
However, it must be taken into account that a poorly done job can greatly affect the feeling of comfort. That is one of its main disadvantages. In addition, the state of the container must be examined carefully. “The base might be rusty because they were used for years,” says Rojas. That is precisely what happened with the houses of La Palma, which rusted four months after being handed over to their owners. For the most reluctant customers, there is another alternative: using modules, also made of steel, but made from scratch. The aesthetic is the same, although they allow for widths of three meters (10 feet) and they are new. Their sheet metal is replaced by insulation. The final price of the houses, however, does not vary much. Whether it is a container or a new module, all that remains is to take it to its destination, which costs between €1,000 and €2,500 ($1,100 to $2,800), depending on how far they must be carried.
Sign up for our weekly newsletter to get more English-language news coverage from EL PAÍS USA Edition